STACK VIBRATIONS
Vc = f * D/S
f – Natural Frequency of stack
D – Diameter at the top
S – 0.2 (unless other structures are nearby)
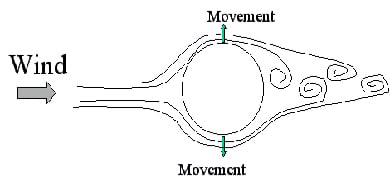
For more information on vortex shedding, check out our article: Take Vortex Shedding Seriously
Since Meca specializes in Stack design, we frequently encounter problems with new and existing stacks experiencing vortex induced vibration. It’s the single biggest problem that faces stack designers. As a result, we began offering services to assist Engineers in solving vortex shedding problems. We can help you with evaluation of a specific stack vibration problem, but here are the common solutions as well as their advantages and disadvantages.
Vortex Shedding Solution | Advantages | Disadvantages |
Damping Pad |
|
|
Tuned Mass Damper (TMD) |
|
|
Tuned Liquid Damper (TLD) |
|
|
Helical Strakes |
|
|
Segmented Strakes |
|
|
I have a vibration problem, what’s next?
If you have a stack with wind induced vibration issues, answer the questions in the “Vortex Shedding Solution Wizard” to receive a recommendation on how to best solve the problem.