Anchor Bolt Pretension
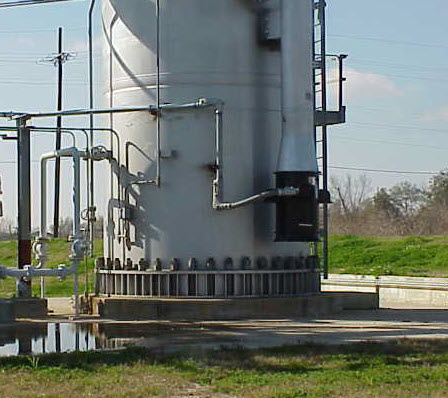
There is nothing simple about recommending anchor bolt pretension, ask ten engineers and you could get eleven different recommendations. Meca has done all of the research in order to try to resolve this topic once and for all…at least until the next anchor bolt pretension recommendation is published. We are definitely not experts on this topic, and so we have tried to break it down into simple guidelines that even we can follow.
Is Anchor Bolt Pretension Necessary?
According to “Wind Loads and Anchor Bolt Design for Petrochemical Facilities” (ASCE, 1997) pre-tensioning of anchor bolts is recommended for the following three situations:
- Tall vessels sensitive to wind, such as towers with a height to width ratio of 15 or more, or more than 100 ft [30 m] tall.
- Dynamic machinery such as compressors or other pulsating equipment
- High-strength anchor bolts to minimize load reversals
Stack anchor bolts don’t typically experience load reversals, because they go from a large tensile stress to an equal compressive stress. Anchor bolts go from no tension/compression to some tension value, and so it’s not a complete load reversal. Many stacks designed by MecaStack meet the first criteria and exceed either 100 ft [30 m] or a height to diameter ratio of 15. According to this criteria many stacks would benefit from anchor bolt pretension.
There are a couple of benefits to pre-tensioning anchor bolts:
1) When cyclical loading is expected, pretensioning helps to minimize the fluctuations in tensile stress within the bolt. This improves the fatigue life because the bolt will remain in tension through the cyclical loading. The pretension creates compression between the baseplate and concrete, and some of the loading goes toward decreasing that compression rather than adding tension to the bolt. This is illustrated somewhat in the graph.
2) Pretension increases the compressive force acting on the concrete, which increases the shear resistance that can be achieved through friction between the baseplate and the foundation. If the shear loads are high, and friction due to dead weight of the structure alone is not sufficient then adding pretension will increase that frictional resistance of shear loads. This could be desirable if you have oversized anchor bolt holes, and the structure could move before the bolts are engaged to resist the shear.
Should I always Pretension?
Reading the guidelines above, it would seem that for tall stacks pretension would always be desirable. Unfortunately, it’s not that simple. In AISC Steel Design Guide 1 “Base Plate and Anchor Rod Design” 2nd edition, they state the following:
Pretensioning the rod can improve it’s fatigue life, but anchor rods can effectively be pretensioned only against steel. Even when tensioning 55-ksi rod, 24 in. long, it only takes concrete creep/shrinkage of 0.05 in to relieve all pretension. Thus, it is recommended, when is necessary to pretension an anchor rod, that a steel sleeve be used that is adequate to transfer the anchor rod pretension from the anchor plate to the baseplate.
This is a very good point, and in our opinion one of the most important determining factors. If there is not a steel sleeve installed in the foundation, then there is really not a good reason to pretension the anchor bolts since it’s unlikely that the pretension will be maintained anyway. If pretensioning is desired and specified, then we believe it is imperative that the anchor bolt be designed with a pipe sleeve as shown to the right. This can be a problem logistically, because often the engineer designing the stack does not necessarily design the foundation.
When to Pretension?
Specifying pretension dictates that a sleeve be installed with the anchor bolts, and that is not always going to be feasible or desireable. We need better criteria to determine exactly when pretension is really necessary. The most common form of cyclical loading on a stack would be due to wind induced vibration (vortex shedding). With most stacks, if vortex shedding has been adequately addressed by using a damper, strakes, etc., then the cylical loading will be minimal. The AISC Design Guide “Base Plate and Anchor Rod Design” once again provides some guidance on this topic:
Column base connections subject to more than 20,000 repeated applications of axial tension and/or flexure must be designed for fatigue. When the maximum fatigue stress range is less than the threshold fatigue stress range, 7 ksi [48.2 MPa], anchor rods need not be further checked for fatigue.
This gives designers some specific guidance on determining when pretension might be necessary. Depending upon which vortex shedding criteria within MecaStack is being followed, some of the design codes estimate the number of cycles expected. Some of these codes might also estimate static equivalent loads and with these loads one could concievably estimate a tensile stress in the bolts. Unfortunately, at the time of writing this article MecaStack does not do these checks automatically, but perhaps someday this will be included.
How Much Pretension?
When pretension is required, there are a variety of opinions on what pretension should be specified. Some engineers recommend setting pretension equal to the maximum tension expected due to the lateral loading and other engineers recommend 50% to 70% of those factored tensile loads. The “Wind Loads and Anchor Bolt Design for Petrochemical Facilities” recommends one-third (1/3) of the ultimate tensile strength of the bolt.
How to Pretension?
If pretension is required here are the most common ways to achieve the pretension:
1) Hydraulic Jacking – Most accurate method and is recommended if hydraulic equipment is available and if the physical clearances are adequate to use the equipment.
2) Turn-of-Nut – This is the easiest to perform and gives reasonably accurate results. Bring to a “snug-tight” condition, and then the nut rotation past snug can be estimated with the following equation.
Nut Rotation Degrees = 360 * L * At * ft * Tlc / (E * Ad)
L = Bolt stretch length, in (mm)
At = Tensile stress area of bolt, in^2 (mm^2)
ft = Desired tensile stress, ksi (kPa)
Tlc = Bolt threads per unit length, threads/in (threads/mm)
E = Elastic modulus of bolt, ksi (kPa)
Ad = Nominal bolt area, in^2 (mm^2)
If it is necessary to retighten the bolt to allow for any loss of pre-load, the nut should be loosened, brought to “snug tight” and then turned the number of degrees calculated.
3) Torque Wrench – Provides only a rough measure of actual pretension load
T = K * D * P
T = Tightening torque, kip-in (KN-mm)
K = torque coefficient, dimensionless (Typically 0.2)
D = Bolt Diameter, nominal, in (mm)
P = Bolt tensile load, kips (KN)
Does Pretension Add to Load on Bolt?
A common misperception is if you apply pretension to the bolt, then when the loading event occurs that the additional stress is added to the pretension. This isn’t actually what happens, the application of load to the bolt only serves to decrease the compressive stress between the baseplate and foundation. The maxium stress on the bolt is not increased when pretension is specified.
Special Requirements for Damping Pads:
When a damping pad is used, all of the pretension recommendations here are no longer applicable. If Meca supplies the damping pad, then we will recommend the pretension that is appropriate to be used with the pad.
Recommendation of a Non-Pretension Anchor Bolt:
If you have decided that pretension is NOT required, then you still may need to give the field installation crew guidance on the anchor bolts. We recommend 1/4 turn from snug-tight. Snug tight is defined by RCSC Specification for Structural Joints using High-Strength Bolts as follows:
The snug tightened condition is the tightness that is attained with a few impacts of an impact wrench or the full effort of an ironworker using a ordinary spud wrench to bring the plies into firm contact.
Bring the bolts to a snug-tight condition, and then turn the nut approximately 1/4 turn past this condition. Although this will place pretension on the anchor bolt, unless steel sleeves are installed we are not considering it to be a pretensioned joint. We are just trying to ensure that the nuts do not become loosened over time. ASME STS-1 then recommends that 30 days after installation, the anchor bolts be retightened.
Conclusion:
If a stack is prone to wind induced vibration, then the first step is to address that problem so that any cyclical loading is minimized. If the number of cycles is expected to exceed 20,000 then either a pretensioned anchor bolt is necessary or the anchor bolts need to be considered for fatigue. When pretension is required, steel sleeves should be installed.
If cyclical loading and fatigue are not a concern, then follow our recommendation for a non-pretensioned anchor, and do not specify pretension on the anchor bolts.